Conventional solution mining, also known as In Situ Leaching (ISL), refers to the artificial extraction of raw material, by pumping superheated water into deposits. The targeted minerals are dissolved, and the brine is pumped to the surface where it is cooled down, dried, and processed.
The process is like heap leaching, where ore is extracted, so a leaching solution can be passed through it. However, solution mining requires no excavation.
Solution mining can be used when the target minerals are at a depth of 1000m or deeper. The ore body should be pure with optimal geological conditions.
An important requirement for solution mining is that the target element and its mineral host must be soluble enough to be dissolved. Only certain minerals can be dissolved by readily available solutions fast enough to make solution mining feasible.
What is solution mining used for?
Salt production
Solution mining is also used for water-soluble salts, notably potash. Superheated water is pumped into the deposit. The potash rich brine is pumped to the surface processing plant where it is evaporated to eliminate water. The remaining salt is then treated.
Depending on the groundwater of the area explored, there are two methods of solution mining to use. If the ore contains high levels of calcium, such as limestone, alkaline (carbonate) leaching is used. Otherwise, acid leaching using sulphuric acid is preferred.
Located in Canada, Belle Plaine is the first and largest solution mine in the world. The mine is owned by Mosaic (NYSE: MOS) and produces potash.

elle Plaine Potash Mine. Source: Shutterstock
Uranium minerals
Solution mining is used for the extraction of uranium minerals. Uranium deposits suitable for in situ recovery occur in permeable sand or sandstones. The deposits are either flat or roll-front within a permeable sedimentary layer. Uranium collects as a coating on the sand grains.
Naturally, these deposits are formed by the flow of groundwater bearing oxidized uranium minerals through the permeable rock. Precipitation of minerals occurs when the oxygen content is decreased. Ultimately, solution mining reverses this process in a short period of time.
Solution mining is utilized for uranium production in countries such as the USA, Kazakhstan, Uzbekistan, Australia and China.
How does solution mining work?
The process of solution mining follows:
- A borehole is drilled to the top of the salt formation
- The production wells are lined with pipes of steel, and the hole is extended to the bottom of the salt deposits. The wells make sure the leaching solution does not migrate away from the production area.
- A hot solution of water, oxygen, and carbon dioxide is injected into the ore body. This causes minerals to detach from the sand and flow toward the production wells.
- The solution is pumped to the earth’s surface and minerals removed by filtration of the saturated brine. The reduced brine is then crystallized at a processing plant, producing sodium chloride crystals. The crystals are dewatered in centrifuges and then dried.
- Any insoluble materials settle in the bottom of the mine and remain underground.
- The water is cleaned and injected back into the ground to repeat the leach cycle.
- Salt domes are used for storage in commercial scale production.
The following diagram shows the ISL process:
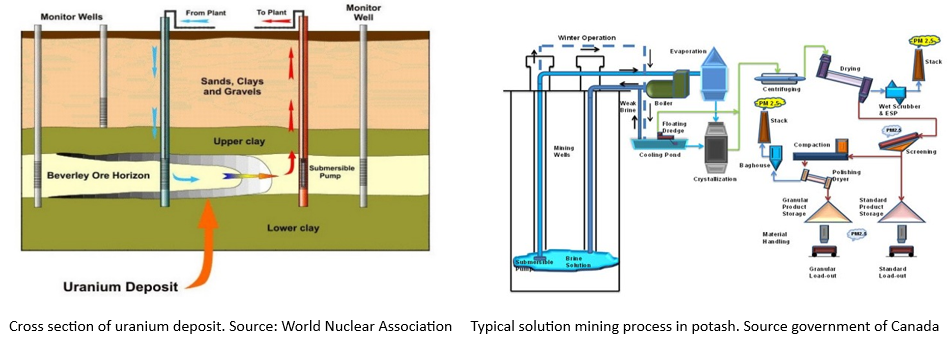
Solution mining techniques are often cheaper than conventional methods, such as open pit or underground mining. The average capital expenditures for a solution mine is US$1,000/t, whereas for an underground mine it is US$1,400/t.
The process avoids large investment costs and the difficult stage of excavating large volumes of materials, which consequently requires less infrastructure and manpower.
Solution mining benefits
Besides the low operating costs of ISL mining, a key benefit is that it is raises less environmental concerns, from both a construction and operations perspective. This method can drastically reduce a company’s carbon footprint.
In contrast, conventional mining can lead to environmental issues, including disturbance to the land where large salt tailings are stored on the surface for many decades, large amount of freshwater usage and a high demand on utilities.
Solution mining disadvantages
One disadvantage of solution mining is the risk of contamination of the ground water and drinking water.
The leaching solution used can have adverse effects on the local water table, bringing with them dissolved metals or minerals. Hence, monitoring wells are utilized as a prevention tool.
In countries such as the USA and Canada, environmental protection acts are implemented to ensure that the groundwater returns to its pre-solution mining condition.
In conventional mining, contact with radioactive material via ore dust or radon release is more likely than in solution mining. However, measures are still implemented to prevent the release of radioactive material. For example, mine workers are monitored for alpha and gamma radiation to comply with guidelines.
In potash mining, specifically, the creation of large salt caverns is common. Gradual collapsing of the rock can happen due to its soft nature, and so only certain areas are suitable and permitted for solution mining.
Alternative mining methods
Underground Mining
Underground mining is an alternative to solution mining for both potash and uranium production. When any orebody lies a considerable distance below the surface underground techniques are considered.
During the traditional underground mining process, tunnel boring machines are deployed to dig out the raw ore, which is then transported to the processing mill at ground level, where it’s crushed and refined to extract the potassium salts from the potash.

Overview of activities for potash conventional and solution mining. Source: Environment and Climate Chane Canada
Open Pit Mining
Besides solution mining, open pit mining is also used to mine uranium. It is a form of surface mining whereby the soil and rock overlying the mineral deposits are removed, and the ore is extracted from the ground through an open pir or burrow. Open pit mines are the most conventional mining method used globally and do not require tunnels.
For uranium, this type of mining is only possible if the ore is near the surface – usually no more than 100m deep.